Just imagine the satisfaction in driving over 1,500 miles (about 2,400 kilometers) with your eco-friendly electric car without having to stop to charge the battery. After all, that’s more than four times the length of the best and most expensive model on the market today.
Under the hood hides a revolutionary new type of battery that, unlike the batteries of conventional electric cars, can also power buses, large trucks and even planes. In addition, manufacturing is much simpler and cheaper than the batteries currently used in millions of electric vehicles around the world – and unlike them, recycling is also easy.
That sounds like a science fiction fantasy? But it is already a reality. Last Friday, the inventor of this ingenious energy cell, British engineer Trevor Jackson, signed a contract to start manufacturing soon.
Trevor Jackson, 58, of Tavistock, Devon, a former Royal Navy officer and father of 8 children, has secured a multi-million pound contract to manufacture the device in the UK on a grand scale.
Austin Electric, an engineering firm based in Essex that now owns the rights to the old logo of the Austin Motor Company, will install thousands of them in electric vehicles next year. According to Austin CEO Danny Corcoran, the new technology is a “game changer” and will change everything.
“It could trigger the next industrial revolution. The advantages over conventional batteries for electric vehicles are enormous, “he said.
Only a few will probably have heard of Jackson’s extraordinary invention. The reason for this, he explains, is that since he and his company Metalectrique ltd. developed a prototype a decade ago, faced with the resolute resistance of automobile manufacturers.
The industry, of course, has every reason not to leave the terrain to a competitor that could eventually make their own technology superfluous. Skeptics in the ranks of the auto industry claim that Trevor’s technology is unproven, and the benefits are exaggerated.
However, an independent assessment from the UK government agency UK Trade and Investment in 2017 revealed that it is a “very attractive battery” based on a “well-established” technology and producing much more energy per kilogram than the batteries of conventional electric vehicles.
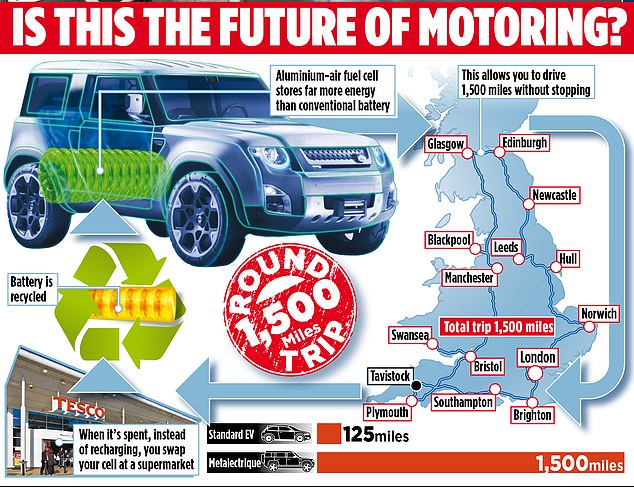
According to Jackson, two years ago, automakers urged the State Department to hold him from a prestigious conference for European companies and governments at the British Embassy in Paris, which should agree on a plan to ensure that all new cars are electrically powered by 2040 , The plan to exclude him, however, failed. With the signing of the agreement with Austin, our inventor seems finally to be on the road to success.
He has also received a grant of £ 108,000 for further research from the Advanced Propulsion Center, a partner of the Department of Business, Innovation and Competencies. Its technology has been validated by two French universities.
He says, “It was a tough fight, but I’m finally making progress. From any logical point of view, this is the way to go. ”
After a remarkable career as an engineer, Jackson began working on new ways to power electric vehicles. He once worked for Rolls-Royce in Derby and helped design nuclear reactors. He then took on a job with the Royal Navy, where he worked as a lieutenant on board nuclear submarines and managed their reactors and waited.
Prior to founding his own company in 1999, he worked for BAE Systems, where he initially sought alternative, environmentally friendly ways to drive vehicles. At this time he married his partner Kathryn. Today the couple has eight children aged 11 to 27 and lives in Tavistock on the edge of Dartmoor in Devon.
In 2001, he began exploring the potential of a technology first developed in the 1960s. Scientists have discovered that by immersing aluminum in a chemical solution called an electrolyte, they can initiate a reaction between the metal and the air to produce electricity. However, the process was initially unusable for commercial batteries because the electrolyte was extremely toxic and corrosive.
After years of experimenting at his workshop in Callington, Cornwall, Jackson came up with the enlightening moment when he developed a new formula for an electrolyte that was neither toxic nor corrosive.
“I drank it when I showed it to the investors so I could prove it was harmless,” says Jackson. Another problem with the 1960s version was that it only worked with pure aluminum, which is very expensive.
But Jackson’s electrolyte works with far less pure metal – including simple recycled soda cans. The top secret formula is the key to his device.
Technically correct, it should be called a fuel cell and not a battery. Anyway, it’s so light and powerful that it could now revolutionize all low-CO² traffic, so much energy does it deliver.
Jackson showed it off. He cut off the top of a soda can, emptied it, filled it with electrolyte, and attached electrodes to power a small propeller. “The energy in here will keep the propeller going for a month,” he said. “You can see what that technology can do to a vehicle if you scale it up.” That’s what will happen after the deal with Austin last week. Three immediate projects are close to the immediate start of production.
The first project is to make some tuk-tuks for the Asian market – three-wheeled mopeds. The second is the production of e-bikes, which will be cheaper and have much more reach than those of competitors in the market.
Finally, and most importantly, the company will produce kits to turn ordinary gasoline and diesel vehicles into hybrid vehicles by equipping them with aluminum-air fuel cells and electric motors on the rear wheels.
The driver can then choose to drive the car on fossil fuels or with electricity. The cost of such a conversion will be around £ 3,500, according to Jackson, and will be available by the beginning of next year. This, according to Jackson, is the springboard for a full-fledged electric vehicle with aluminum-air fuel cells. The auto industry has already invested heavily in a completely different type of battery, lithium-ion.
Lithium-ion batteries are also rechargeable in devices such as computers and cell phones. Almost every electric vehicle on the road uses them. However, they have very big disadvantages. Thus, in addition to lithium, they contain rare, toxic substances such as cobalt. They can explode or catch fire, as we saw in the numerous incidents that forced Samsung 2016 to recall tens of thousands of Galaxy Note 7 phones.
Repeated charging ultimately consumes car-sized models. Their recycling to recover cobalt and lithium is extremely costly – about five times the cost of simply disposing of it as waste plus re-manufacturing.
Aluminum, on the other hand, is the metal most commonly found on the planet. Many factories refining it from ore or recycled waste are using green, renewable energy, such as hydropower dams.
And once an aluminum air fuel cell is used up, it can be recycled very cheaply. According to Jackson, the low cost of recycling means that the cost of running an aluminum-air fuel-cell car is as low as 13 cents per kilometer. For comparison, the cost of a small hatchback gasoline car amounts to about 22.5 cents per kilometer. More importantly, lithium-ion batteries are heavy weight.
Accredited testing has shown that Jackson’s fuel cell produces nine times as much energy as lithium-ion: that’s nine times the kilowatt-hours of electricity per kilogram. Luxury electric car maker Tesla claims its model S to have a range of 370 miles per charge. According to Jackson, the range would be 2,700 miles if you were driving the same car with an aluminum-air fuel cell that had the same weight as the lithium-ion battery.
Aluminum-air fuel cells also take up less space. Jackson points out that if the Tesla were equipped with an aluminum-air fuel cell that was the same size as its current battery, it would be able to drive an impressive 1,500 miles without interruption. An average British family whose car travels 12,000 km a year (and statistically looks similar in other countries) would only have to change their fuel cell a few times a year.
Scientists describe the ratio of weight to energy as energy density. According to Jackson, aluminum-air fuel cells could be used in buses or large trucks because they have a much greater density than lithium-ion batteries. If such vehicles were powered by lithium-ion energy, they would be impractically heavy, since the battery then weighs much as much as the freight.
He says, “You could easily pair many of our cells together in such a vehicle – after all, you’ve gained a lot of space by removing the diesel tanks.” Jackson adds that aluminum-air cells could also be used on airplanes. “We are currently in talks with two aircraft manufacturers. It will not be suitable for jets. But it would work in propeller aircraft and be suitable for short-haul passenger and cargo flights. ”
Meanwhile, the raw cost of a new aluminum-air cell is much lower. In a Tesla, Jackson explains, the battery costs about £ 30,000. An aluminum-air fuel cell that drives the same car for longer would only cost £ 5,000.
Motorists relying on lithium-ion batteries need to charge their batteries from the mains after consumption – a process that takes a long time, often overnight. If, on the other hand, an aluminum air cell is exhausted, the driver simply exchanges it for a new one.
Instead of a huge network of charging stations, only shops are needed in which empty cells can be exchanged for charged ones, just as people today are already exchanging propane gas bottles.
Replacing a fuel cell takes about 90 seconds, according to Jackson. He and Corcoran point to the “advanced stage” of talks with two major supermarket chains to provide this service.
Last week, Sir James Dyson announced that he was going to reject his plans to manufacture electric cars because he concluded they were not economically viable, even though he had already invested millions.
“The problem is,” says Jackson, “that Dyson used lithium-ion. If his cars were equipped with aluminum-air fuel cells, the result could have been different. ”
Ironically, Jackson’s story has more than a passing resemblance to Dyson’s.
Dyson had developed his bagless vacuum cleaner in a workshop at his home, supported by his wife.
And just as Jackson had to fight against the interests of the big automakers, Dyson needed ten years to make an economic breakthrough, as neither a distributor nor an existing manufacturer was willing to disrupt the lucrative market for vacuum cleaner bags.
“Everyone knows that transport is the hardest nut to crack if we really want to achieve the government’s goal of not emitting greenhouse gases by 2050,” says Jackson. “We will not reach that with lithium ions. Apart from all other aspects, lithium-ion is of no use to trucks burning huge amounts of fossil fuels.
“I know we are fighting against deep-seated interests, but the technological and environmental benefits of aluminum-air are overwhelming – and Britain has a chance to become a world leader.”
Corcoran adds, “If you want to do something for the environment, you can. You can do it now with this product.”
Related articles:
Tesla’s Blade Runner-like Pickup Outperforms Porsche 911, F-150 – And Is Affordable For Everyone
Tesla Killer Is Here: Fisker Patents 500-Mile Range Car Battery That Charges In One Minute
Electric Car With Solar Cells: Manufacturer Promises 800 Kilometers Range
This Car Is Powered By Salt Water: 920HP, Top Speed 217.5 MPH, 373 Miles/Tank